This paper presents an experimental investigation on a new configuration of film cooling hole, namely the near surface streamwise diffusion (NSSD) hole. A discrete streamwise diffused shallow submerged structure is constructed on the exit of a simple cylindrical hole. There is a middle bulge at the exit edge of the shallow submerged structure to expand the coolant laterally. The adiabatic film cooling effectiveness was measured using pressure sensitive paint (PSP) technique on a flat plate model. The experiment was performed under density ratio DR = 1.38 and the blowing ratio M = 0.5–2.5. A simple cylindrical hole and a typical fan-shaped hole were chosen to be the baseline holes to be compared with NSSD hole. Six NSSD hole cases were tested and compared to investigate the influence of geometrical parameters. The experimental results showed that the cooling effectiveness of NSSD hole was significantly higher than the simple cylindrical hole but was slightly lower than the fan-shaped hole. The streamwise diffused shallow submerged structure can effectively expand the coolant laterally and can keep film attached to the surface under high blowing ratio. Due to the special flow mechanism, the laterally averaged cooling effectiveness of NSSD hole exhibited a ladder-style decreasing trend where the cooling effectiveness far downstream is close to the fan-shaped hole. The change of geometrical parameter of the near surface streamwise diffusion structure results in the obvious variation of cooling effectiveness especially at the high blowing ratio conditions. A smaller streamwise spacing between the middle bulge and the exit edge
of the cylindrical hole can enhance the interaction between the coolant and the middle bulge, which is conducive to the increase of cooling effectiveness.
Conclusions
The adiabatic film cooling effectiveness of a near surface streamwise diffusion hole was presented for flat plate experiments by the pressure sensitive paint measurement technique. The experiments were performed under density ratio DR = 1.38 and blowing ratio M = 0.5–2.5. A comparative study was performed between a simple cylindrical hole, a typical fan-shaped hole and six NSSD hole cases. The conclusions are as follows:
The near surface streamwise diffusion structure constructed on the exit of a cylindrical hole can enlarge the film coverage width greatly and increase the film cooling effectiveness significantly. The overall cooling effectiveness of NSSD hole rises gradually along with the augment of blowing ratio from M = 0.5 to M = 2.5. Compared with the fan-shaped hole, the spatially averaged cooling effectiveness of the NSSD hole is slightly weaker. In the region close to the hole (about x/D < 10), the laterally averaged cooling effectiveness of NSSD holes is obviously lower than that of the fan-shaped hole. By contrast, in the region far from the hole (about x/D > 10), the laterally averaged cooling effectiveness of NSSD holes is close to that of the fan-shaped hole.
The key of near surface streamwise diffusion structure is the middle bulge on the exit edge. The middle bulge forces the coolant to diffuse laterally. At the meantime, the coolant from the cylindrical hole impinging the bulge generates a strong down-wash vortex pair, which is conducive to the coolant attachment to the protected surface and spreads to far downstream. Since the main body of NSSD hole is a cylindrical hole, the coolant exit velocity is much higher than that of the fan-shaped hole, which makes the coolant maintain high cooling capacity at far downstream. The cooling effectiveness distribution of NSSD hole is a bi-peak pattern at near downstream, but it turns into a single-peak effectiveness pattern within a short streamwise distance. The coolant flowing over the middle bulge provides cooling effectiveness supplement for the vicinity region of hole centerline. The geometrical parameter variation of the near surface streamwise diffusion structure has palpable impacts on cooling effectiveness, especially at the high blowing ratio, i.e., M = 2.0. Moreover, the exit edge surface shape and streamwise length of middle bulge are interrelated. A combination of greater streamwise length of the middle bulge and the curved exit edge surface produces higher laterally averaged cooling effectiveness. The smaller spacing between cylindrical hole and exit edge middle bulge is conducive to yielding higher cooling effectiveness. The large exit edge incline angle is a major contributor to the increase of cooling effectiveness at far downstream when the exit edge surface is a plane.
The results have been published on International Journal of Heat and Mass Transfer 103 (2016) 1–13.
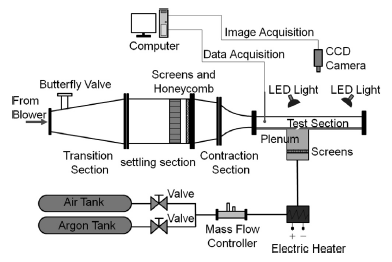
Fig. 1. Experimental facilities.