Wind energy is a kind of widely distributed, renewable, clean energy. Compared with other forms of energy, wind energy has many advantages, such as no pollution, small occupation, and little negative impact on the environment. Moreover, It can provide an important way to replace the fossil fuels.
According to the computation time and the complexity of the model, existing wind turbine aerodynamic calculation model can be divided into three categories, CFD (Computational Fluid Dynamics) model, the vortex method model and BEM (Blade Element and Momentum Model) model, respectively. The strength of CFD model lies in providing a detailed 3D flow field of wind turbine and wind turbine aerodynamic performance. However, CFD model has not been widely used in the design of wind turbine blades since the flow field is multi-scaled and the existing CFD 3D model requires huge computing resources and computing time. In vortex method model, the blade attachment vorticity in 3D flow field is abstracted to be concentrated line vortices and eddies, thus, the wind turbine aerodynamic performance can be analyzed combined with rigid or free wake model. Although simplifying the 3D flow field calculation contributes to improving the computational efficiency of the aerodynamic performance, it brings difficulties to calculate and characterize the pressure distribution of the blade surface and the development characteristics of the wake flow. As the most widely used pneumatic calculation model in engineering applications, BEM model, which is based on 1D momentum theory and 2D blade element theory, can realize closed calculation with the use of 2D experimental airfoil lift and drag coefficient. Its advantages lie in the calculation speed, while its shortcomings lie in the need for people experience corrections.
In order to improve the calculation and analysis capabilities of the existing models, the Wind Turbine Blade R & D (Experimental) Center, IET, made vortex method model as the main breakthrough and created a new model for engineering applications on the basis of existing models. With the model, not only the 3D flow field of leaf surface can be obtained, what’s more, the model, which does not need a long computation time, is suitable for engineering applications. The team carried out research on the surface element model and corresponding free wake model and developed a viscous inviscid coupling model combined with the development of the boundary layer model.
The model, featuring in getting the blade surface pressure and viscous force distribution, can improve the analytical capacity of the 3D flow field in maximum extent. Point source, dipole intensity distribution as well as 3D potential flow streamlines for NREL Phase VI wind turbine blades, which was calculated through the viscous inviscid coupling model, are shown in Figure 1. In addition, in view of the important implications of large scale wake structure on the 3D aerodynamic performance, the research team combined the element model with the 3D surface actuation model, on one hand which can provide volume force distribution for 3D actuator CFD calculation using the quickly calculation characteristics of the surface element; on the other hand, it can simulate the development of wind turbine wake vortex based on the actuation large-scaled model and high-precision CFD model. Velocity and vorticity distribution within the plane of the wind wheel calculated with actuator line model are shown in Figure 2. The research team, taking advantages of the characteristics of existing computational models to construct large-scale aerodynamic analysis model, provided an important complement to the development of wind turbine aerodynamic model, and laid an important foundation for the design of wind turbine blades.
The research was supported by the National Natural Science Foundation of China, with relevant results received by the Renewable Energy in 2012.
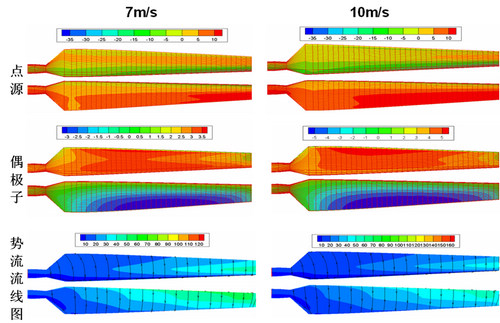
Fig. 1. The calculate results of viscous inviscid coupling models for NREL Phase VI wind turbine blade
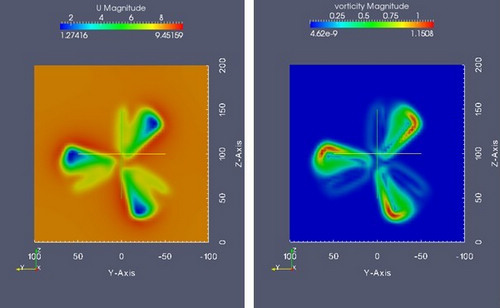
Fig. 2. Velocity and vorticity distribution within the plane of the wind wheel calculated with actuator line model